Tunnel shotcreting robot
|
1.Main Contents
1.1Brief Introduction
This project plans to focus on the following aspects: Complex and variable large space tunnel environment scanning modeling technology, Trajectory planning techniques that constrain multiple targets, Nonlinear strongly coupled multi-joint manipulator control and vibration suppression technology, and Device remote monitoring management technology under restricted channel. A point cloud denoising algorithm based on normal deviation and a hole repair algorithm based on triangulation were proposed to overcome the influence of dust, humidity and vibration on the scanning modeling of sensors. A combination of point cloud search, point cloud feature extraction and segmentation is adopted to identify the arch, protective net, back break and other feature structures on the surface of the tunnel during construction, and adjust the shotcreting pattern adaptively. The tunnel shotcreting task was modeled as a multi-objective optimization problem of operation time-rebound rate, and the multi-objective differential evolution algorithm based on multi-strategy sequencing variation was used to solve the optimal shotcreting trajectory, and the shotcreting operation of the tunnel surface was completed with the highest efficiency and the lowest loss. A sliding mode control method based on double fuzzy adaptive control is proposed, which has the advantages of short adjustment time, high tracking accuracy and strong robustness. In this paper, a design method of feed-forward feedback controller based on large disturbance and large time delay is proposed to establish an estimator of the disturbance force on the boom, and to solve the problems of boom vibration and terminal slopping caused by load change, external disturbance and motion characteristics of the wet sprayer during operation.
1.2Purposes
1)Identification and modeling of construction surface
2)Trajectory planning of automated construction operations and intelligent injection operations
3)Remote monitoring and management of tunnel construction equipment
1.3Significance
1)With the province's relevant areas of strategic emerging industries in-depth integration
2)Achieve major technological breakthroughs and promote industrial restructuring
3)We will improve the overall competitiveness and level of the industry
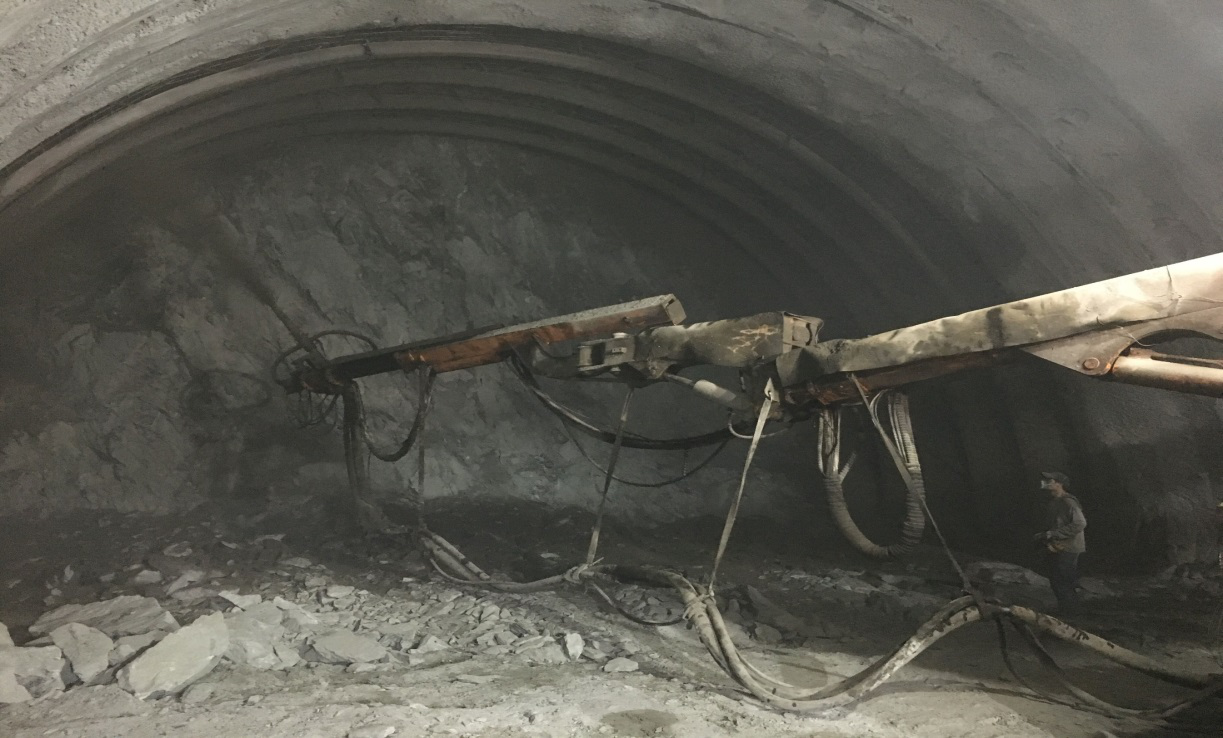
|
2.Project research progress
1.Forward and backward kinematics modeling of tunnel spraying manipulator
2.Study on environmental scanning modeling technology of complex and variable large space tunnel
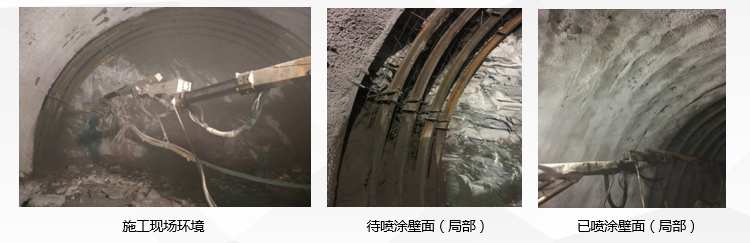
3.Research on trajectory planning technique of constrained multiple targets
In this project, combined with the actual spraying operation, a multi-strategy differential evolution algorithm based on fast non-dominated sequencing was used to solve the constrained time-resilience multi-objective problem
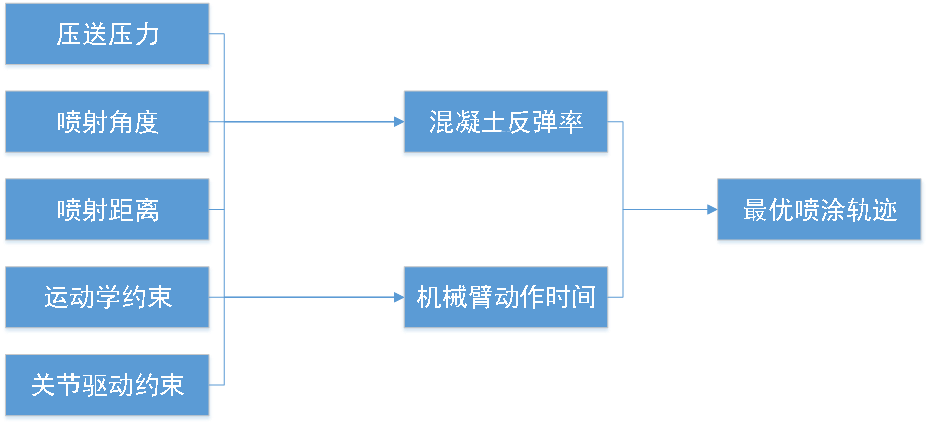
4.Research on manipulator control technology and vibration suppression technology
Trajectory tracking technology of multi-joint manipulator based on adaptive double fuzzy sliding mode control
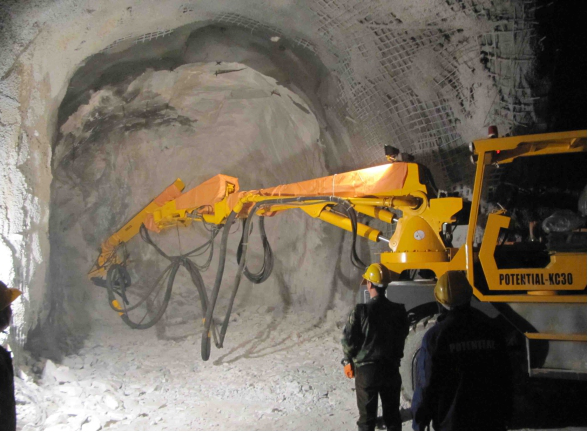
Research on vibration suppression technology of arm frame based on feedforward interference estimation
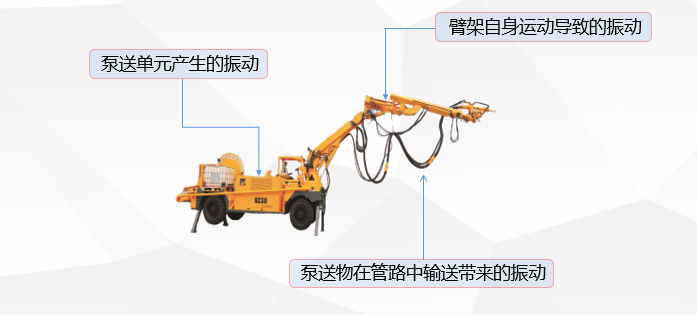
5.Development and application of remote monitoring management platform for tunnel construction equipment
|
Copyright Announcement
Please respect our original works. When reproducing, please mark the original source of the article and the author's information. If you have any questions or ideas to communicate with us, please contact us by email or telephone at the bottom of the page.
|
|